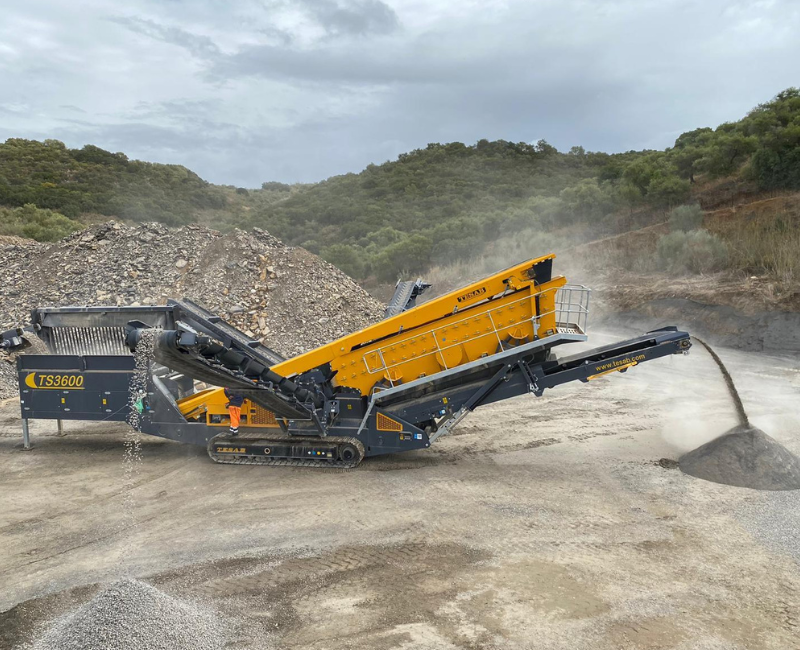
Screeners Explained: Enhancing Performance with Cutting-Edge Screener Technology
At Stewart Plant Sales, we pride ourselves on offering a comprehensive range of material processing equipment, including crushers, screeners, and stackers from renowned manufacturers such as Tesab and Lippmann. In this blog, we will delve into screeners, examining how they work, the benefits they provide, and an overview of the models we have available.
What is a Screener?
Screeners are indispensable tools used across various industries, including mining, recycling, aggregates, and agriculture. They ensure efficient and accurate separation of materials such as soil, sand, or gravel. While screeners can operate as standalone units, they are often integrated into a processing train alongside crushers and stackers to maximise productivity and efficiency.
Accurate material separation post-crushing is as crucial as the crushing process itself. Our range of Tesab, Lippmann, and McCloskey Environmental screeners excels at extracting clean materials from secondary crushing processes, handling materials such as stone, concrete, and chips.
How does a Screener work?
There are four main stages to the screening process:
- Feeding – Raw material is fed into the screener.
- Vibration –When the machine is powered the screener vibrates which makes the material move across the screens.
- Separation - As the material moves, smaller particles pass through the holes in the screen, while larger particles remain on top.
- Collection - The separated materials are collected in different outputs for further processing or use.
H2: What are the Main Parts of a Screener?
- Feed Hopper – The starting point where raw material is loaded. Available in various sizes depending on the model.
- Vibrating Screen Decks – These decks separate material into desired sizes. Typically made from wire mesh, perforated metal, or punched plates, the screens are inserted in tiers within the screener chassis. When powered, the screens shake, allowing the chosen sizes of the product to fall through the gaps and be screened out.
- Double Deck Screeners can sort two sizes of products and an oversize.
- Triple Deck Screeners can produce three different sized products. Fine screening screens are usually inclined, enabling non-falling material to tumble onto a conveyor for further processing.
- Discharge Chutes – Once sifted, the material exits the screener for use or additional sorting.
H2: Tesab Screeners: Engineered to Last
Choosing a Tesab screener means investing in a reliable, versatile, and customisable machine. Available from Stewart Plant Sales are:
- TS2430 - a two-deck screener, matching capacities of some of its larger competitors with a maximum feed size of up to 500 TPH. Outstanding formation of its hydraulic screenbox reduces maintenance in turn, decreasing costs and downtime.Download Brochure.
- TS2600 – a market leading, extremely advanced 20’ x 5’ two-deck screener, incredibly adaptable to the toughest environments due to the angles of its adjustable screenbox. Download Brochure.
- TS3430 – the triple deck version of the TS2430 excels in many applications, especially fine sand screening, providing even higher quality screened products. The high-quality components of this machine’s build make it one of the most dependable on the market. Download Brochure.
- TS3600 – with the huge success from the TS2600, the triple-deck TS3600 takes capacity and performance to another level. The third deck screenbox addition, as well as a cross conveyor and fourth product conveyor, will provide you with ore return for your investment.Download Brochure.
H2: Lippmann Screeners: Setting Industry Standards
We offer two high-quality, innovative Lippmann screeners at Stewart Plant Sales:
- L520s-3 – A three-deck screener designed for high productivity and efficiency, meeting diverse screening needs.
- L622s-2 – One of the world’s largest track mobile screeners, known for its reliability and high-quality production capabilities.
By choosing our cutting-edge screeners you ensure your material processing operations are efficient, reliable, and tailored to your specific needs. Explore our range and discover how our technology can enhance your performance. For more information, visit our screeners page or contact us today to speak with an expert.